Organigramme d’une station de concassage
Une station de concassage est une installation industrielle essentielle pour transformer des matériaux bruts (roches, graviers, etc.) en granulats de différentes tailles, utilisés dans la construction, les travaux publics ou l’industrie. Son organigramme décrit l’organisation des équipements, des processus et des flux de matériaux. Voici une analyse détaillée de sa structure typique.
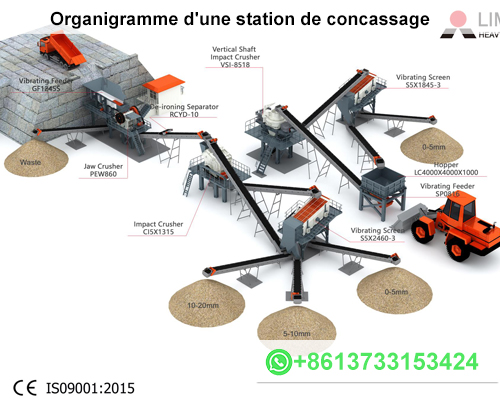
1. Introduction à la station de concassage
Une station de concassage comprend plusieurs étapes mécanisées visant à réduire la taille des matériaux et à les trier selon des spécifications précises. Son organigramme se divise en trois phases principales :
- Réception et préparation des matières premières
- Concassage et criblage
- Stockage et expédition des granulats.
2. Organigramme détaillé
A. Réception des matériaux bruts
- Zone de déchargement : Les camions déversent les blocs de roche ou les graviers dans un chargeur ou une trémie d’alimentation.
- Pré-criblage : Un premier tamisage élimine les particules fines ou les impuretés avant le concassage.
B. Concassage primaire
- Concasseur primaire (à mâchoires, giratoire ou à percussion) : Réduit les gros blocs en éléments de 100 à 300 mm.
- Convoyeurs à bande : Transportent les matériaux vers l’étape suivante.
C. Concassage secondaire et tertiaire
- Concasseur secondaire (à cône ou à percussion) : Affine les granulats à des tailles de 20 à 100 mm.
- Concasseur tertiaire (si nécessaire) : Produit des granulats fins (≤ 20 mm).
D. Criblage
- Tamis vibrants : Classent les granulats par taille (ex. : 0/4 mm, 4/10 mm, 10/20 mm).
- Retour des refus : Les matériaux non conformes sont renvoyés vers les concasseurs.
E. Stockage et expédition
- Silos ou stock à ciel ouvert : Séparent les granulats par calibres.
- Chargement des camions : Les produits finis sont acheminés vers les clients.
3. Équipements clés et leur rôle
- Trémie d’alimentation : Régule l’apport de matériaux.
- Concasseurs : Adaptés à chaque étape de réduction de taille.
- Convoyeurs : Assurent la continuité du flux.
- Tamis et cribles : Garantissent la qualité des granulats.
- Système de contrôle automatisé : Supervise les paramètres de production (débit, taille, etc.).
4. Gestion des flux et sécurité
- Optimisation des déplacements : Les convoyeurs minimisent les manipulations manuelles.
- Mesures anti-pollution : Systèmes d’aspiration des poussières et bassins de décantation pour les eaux usées.
- Sécurité des opérateurs : Équipements de protection, signalisation et formations obligatoires.
5. Enjeux techniques et environnementaux
Une station de concassage moderne intègre des technologies pour :
- Réduire la consommation énergétique (ex. : concasseurs à haut rendement).
- Limiter les nuisances sonores (capots acoustiques).
- Recycler les déchets (réutilisation des refus dans d’autres processus).
Conclusion
L’organigramme d’une station de concassage reflète une logistique industrielle précise, alliant efficacité mécanique et respect des normes environnementales. Chaque composant joue un rôle clé dans la production de granulats, indispensables pour répondre aux besoins croissants des infrastructures urbaines et routières. Une conception optimisée de cette chaîne permet d’améliorer la productivité tout en réduisant l’impact écologique.