petites unités de traitement de minerais
Le traitement du minerai est une chaîne d’applications de traitement qui transforme le minerai brut en concentré de haute qualité (concentration de minerais) puis en minéral pur ou en métal. Le minerai raffiné est utilisé dans les équipements et machines de fabrication de nombreuses industries, ou est vendu dans l’industrie, le commerce et les industries de consommation.
Pour y parvenir, le traitement du minerai sépare les différentes caractéristiques minérales à l’aide de diverses méthodes de traitement du minerai (traitement du minerai). Les principaux processus sont le concassage et le broyage du minerai, le calibrage et la séparation du minerai. Pour séparer le minerai en tailles applicables pour un traitement ultérieur, on utilise le criblage, la classification, la séparation par concentration, la séparation par milieu lourd, la séparation par gravité et/ou magnétique et les applications de flottation.
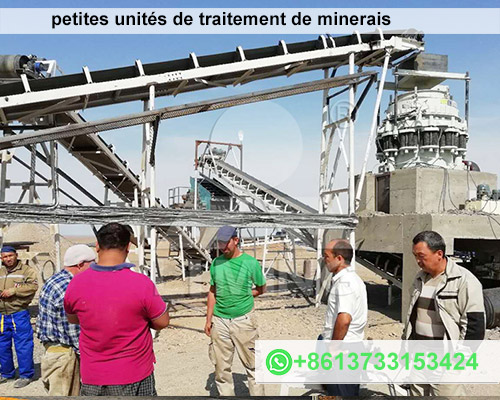
Après ces processus, il est nécessaire de séparer le minerai du concentré produit ou de la gangue (déchet). C’est ce qu’on appelle la déshydratation et cela permet de recycler et de réutiliser l’eau utilisée dans les processus de séparation du minerai. Elle est ensuite envoyée vers des usines de traitement pour un traitement ultérieur.
Méthodes de séparation du minerai
Le tri du minerai dans le traitement des minéraux consiste à séparer le minerai en fonction de sa taille après le concassage et le broyage du minerai. Il existe plusieurs méthodes pour le tri du minerai dans le traitement des minéraux. Selon le minéral traité, certains peuvent nécessiter plus d’une méthode avant d’être déterminés comme étant prêts pour le prochain processus de valorisation du minerai. Les méthodes les plus fréquemment utilisées pour séparer le minerai sont :
- Criblage : les matériaux grossiers subissent un criblage et en utilisant un certain nombre de sections de tamis de différentes tailles, plusieurs minerais de tailles différentes peuvent être produits. Le criblage est également utilisé pour produire une taille d’alimentation aussi uniforme que déterminée par l’opération de traitement suivante.
- Classification : le tri des particules en fonction de leur vitesse de sédimentation dans un fluide est appelé classification, où les différences de taille, de forme et de densité d’un minerai entrent en jeu. Les classificateurs séparent les matières grossières et fines et, bien que la séparation par taille de minerai soit l’objectif principal, la séparation des minéraux par densité est également réalisée.
- Séparation par concentration : la concentration des minerais en tant que méthode de séparation du minerai utilise la concentration en minéraux précieux pour déterminer si le minerai contient des minéraux précieux et les sépare de ceux qui contiennent des particules de gangue. Les minéraux précieux sont séparés en un concentré et en une gangue en un produit de résidus. Cette méthode permet de maximiser la récupération des minéraux précieux à une teneur qui peut être ultérieurement traitée ou vendue.
- Séparation en milieu lourd / séparation en milieu dense : ce type de séparation est généralement utilisé pour la préconcentration des minéraux avant le broyage final. Ce processus repose spécifiquement sur les différences de densité minérale. Le minerai mixte est ajouté à un liquide dont les niveaux de densité se situent entre ceux des deux minéraux, et le minéral le plus lourd coule, tandis que le plus léger flotte.
- Séparation gravitationnelle : la force gravitationnelle générée par la machine permet la séparation des minéraux. La séparation se produit par le mouvement des particules en réponse aux forces gravitationnelles et à la résistance appliquée par le fluide utilisé pour le processus de séparation. Il s’agit d’un type de séparation rentable.
- Séparation magnétique : cette méthode est utilisée lorsque l’un des composants minéraux présente une forte susceptibilité magnétique, il peut être séparé des autres.
- Flottation : la flottation est utilisée en tirant parti des différences de propriétés physico-chimiques de surface des différents minéraux. Les réactifs chimiques ajoutés à la pulpe réagissent de manière sélective avec la surface des particules de minerai précieux et la rendent non mouillable (hydrophobe). Cela leur permet de se fixer aux bulles d’air et, en incluant un agent moussant, de former une mousse stable à la surface de la pulpe.
Quelles sont les étapes du traitement des minéraux après l’extraction du minerai ?
Immédiatement après l’extraction, le minerai est concassé et broyé, ce que l’on appelle la comminution. Cela réduit le minerai en particules de taille gérable et libère ses composants précieux tout en éliminant le minerai non précieux, appelé gangue. Pour une comminution efficace, le minerai de grande taille est broyé dans un concasseur développé pour ce processus spécifique, et le minerai plus petit qui en résulte est obtenu à l’aide de broyeurs en acier rotatifs.
Une fois le minerai de taille gérable en main, le reste des étapes de traitement du minerai est déterminé par le type de minerai. Les schémas de traitement du minerai précisent la méthode de traitement la plus appropriée pour chaque minéral.
Traitement du minerai de cuivre
- Pour l’extraction du minerai de cuivre, le stock de ROM est acheminé vers une usine de traitement du cuivre et commence par un échantillonneur à marteau et un aimant à bande pour l’échantillonnage et l’élimination des débris métalliques
- Broyeur SAG et trommel tamis pour broyage
- Le processus de séparation commence à l’aide d’un groupe de cyclones à haute capacité
- Les particules au-dessus du point de coupure stipulé sont envoyées vers un broyeur à boulets secondaire et un tamis à trommel pour un broyage plus poussé
- Les particules en dessous du point de coupure subissent un traitement de flottation primaire et secondaire
- Transferts finaux de la boue vers le réservoir d’alimentation et l’échantillonneur de boue
- La boue est transférée vers le bassin d’épaississement du concentré
- Enfin, déshydratation et filtration
Traitement de l’or
- Les méthodes d’extraction de l’or à partir du minerai, ou de valorisation de l’or, commencent par le transport de la matière résiduelle du stock vers l’usine de traitement du minerai d’or sous un aimant pour l’élimination des impuretés et son acheminement vers un concasseur à cône
- Le criblage et l’échantillonnage suivent avant d’être dirigés vers un circuit cyclonique où ils subissent un broyage et un criblage via un broyeur à boulets et un tamis à trommel
- La boue résultante est transférée vers un bassin d’épaississement pour la floculation et l’échantillonnage ultérieur
- Il est maintenant temps de procéder à la lixiviation au cyanure de l’or (lixiviation de l’or ou cyanuration de l’or) et au chargement ultérieur en carbone via un tamis intermédiaire
- Le carbone attaché à l’or est éliminé sur un tamis à charbon régénéré et la boue est transférée pour le criblage résiduel et échantillonnage
- Une séparation supplémentaire se produit par flottation et concentration par gravité
Traitement du minerai de fer
- Pour l’extraction du minerai de fer, l’usine de traitement du minerai de fer reçoit du ROM où il subit un concassage puis un criblage sur un tamis à grille.
- Il est ensuite calibré et le minerai au-dessus du point de coupe est envoyé pour un concassage supplémentaire et un calibrage supplémentaire
- Les matériaux grossiers sont éliminés par un aimant à bande supérieure et dans un tambour DMS
- Les déchets grossiers sont envoyés vers un drain et Traitement du minerai de zinc
- À partir du ROM, le minerai subit un concassage primaire avant d’être envoyé au broyage via des broyeurs SAG et à boulets
- Il est ensuite calibré et trié via un groupe de cyclones et envoyé à la flottation où le cuivre et le zinc sont séparés
- Le zinc subit une agitation et une flottation tandis que le cuivre restant subit un rebroyage et une flottation plus propre pour une extraction supplémentaire du zinc
- La boue de zinc subit maintenant un rebroyage et une flottation plus propre pour un tri supplémentaire. L’agitation et la flottation sont répétées jusqu’à ce que la composition requise soit atteinte.
- La boue est transférée vers des cuves d’épaississement et un filtre-presse pour la déshydratation.
- Le concentré de zinc est retiré et est prêt pour le processus de fusion.